Chemical Pilot Plant at Temasek Polytechnic set to advance efforts in sustainable waste management
Post Date: 11 Jun 2024
Temasek Polytechnic (TP) launched Singapore’s first industry-standard Chemical Pilot Plant (CPP) housed in an institute of higher learning that can convert waste cooking oil into biodiesel. The CPP demonstrates TP’s commitment in developing environmentally sustainable initiatives to contribute to our nation’s vision of achieving net zero carbon emissions by 2030.
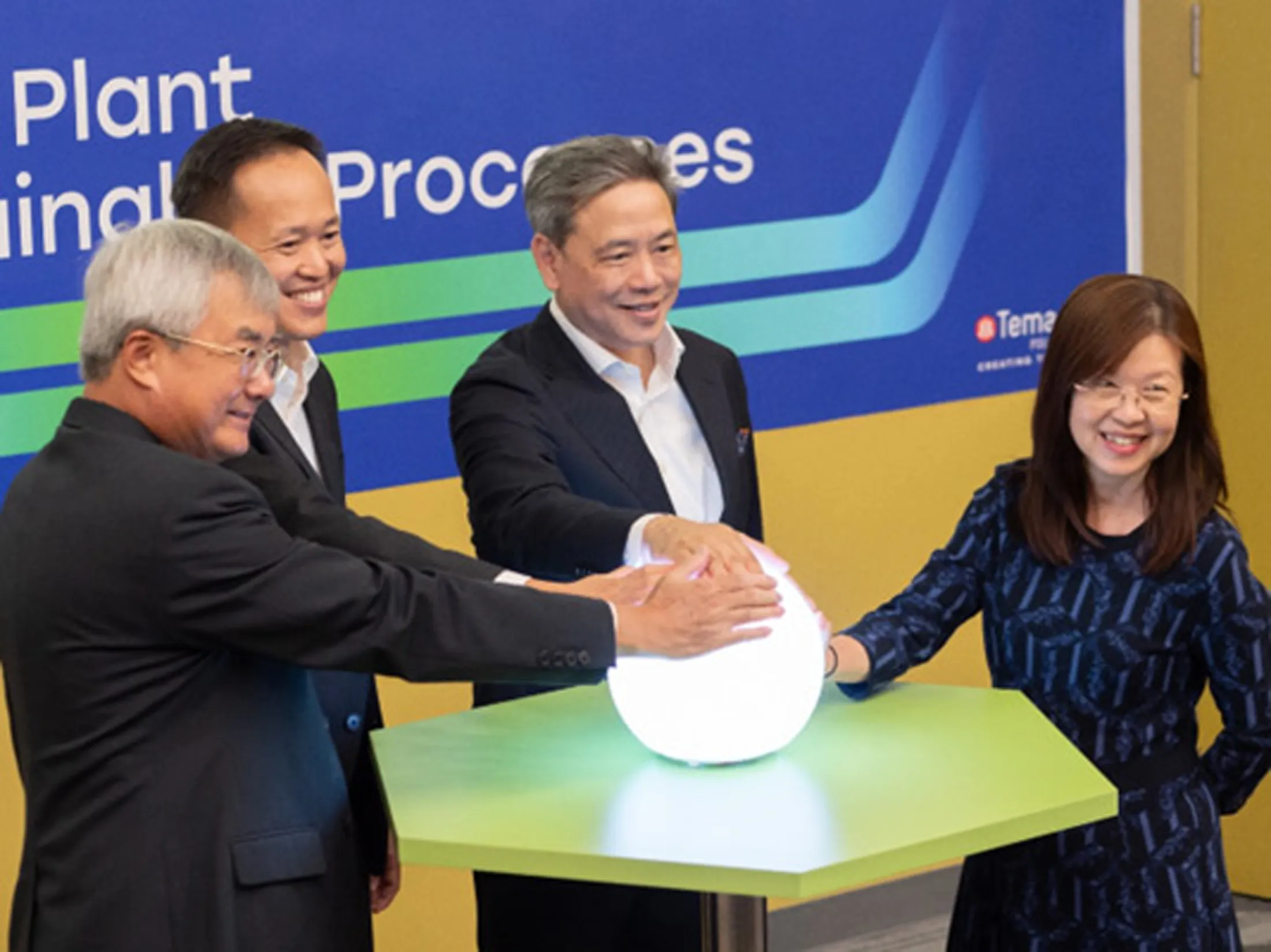
The integrated CPP was built with a vision of equipping learners with the necessary skills for the future economy. This cutting-edge facility is designed to simulate up-to-date industry operations, adhering strictly to industry standards whilst providing real-world, hands-on application training for students enrolled in the Diploma in Chemical Engineering.
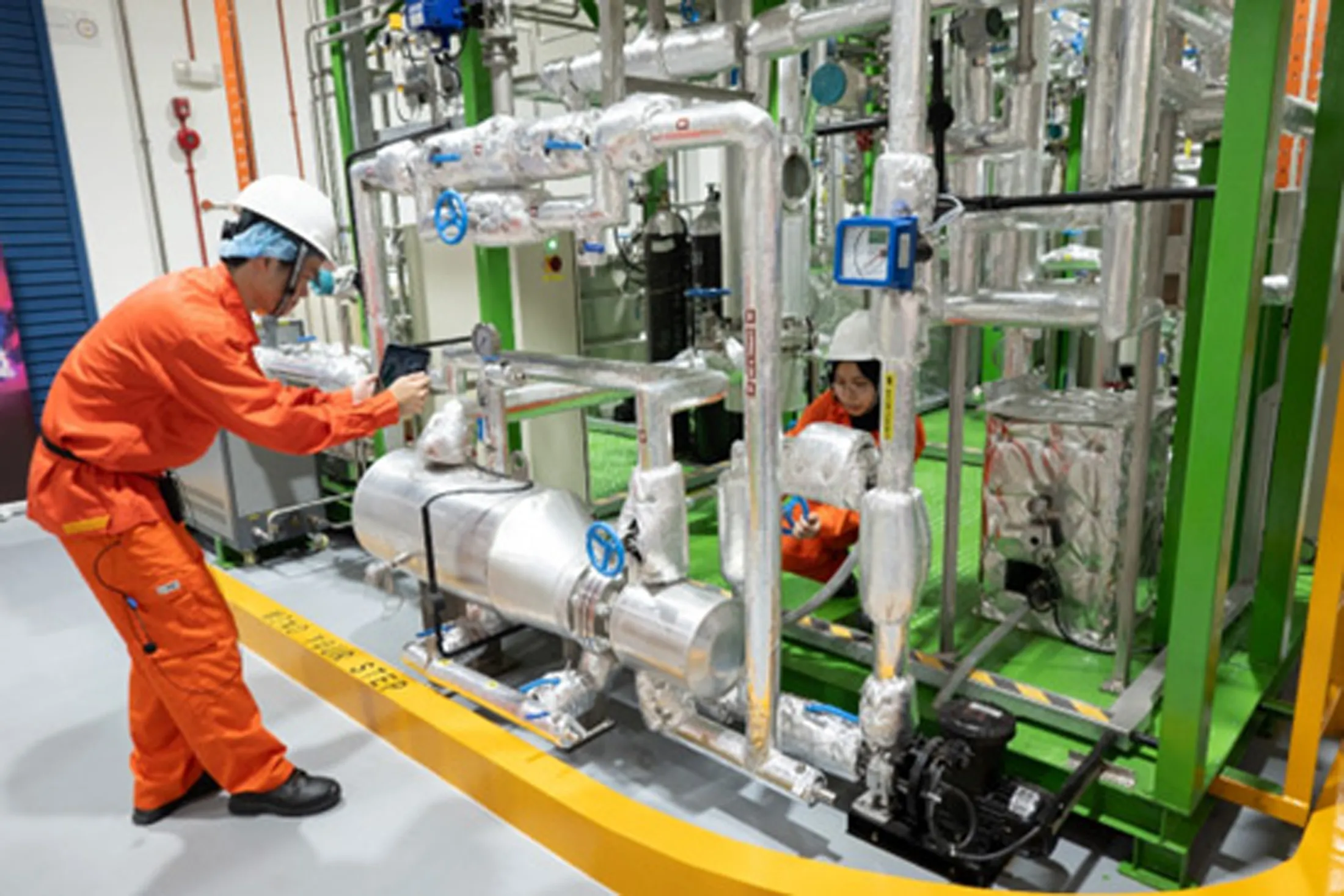
An official service agreement has been signed between TP and Alpha Biofuels to collaborate in producing this biodiesel. Please refer to Annex A for a media factsheet about the CPP.
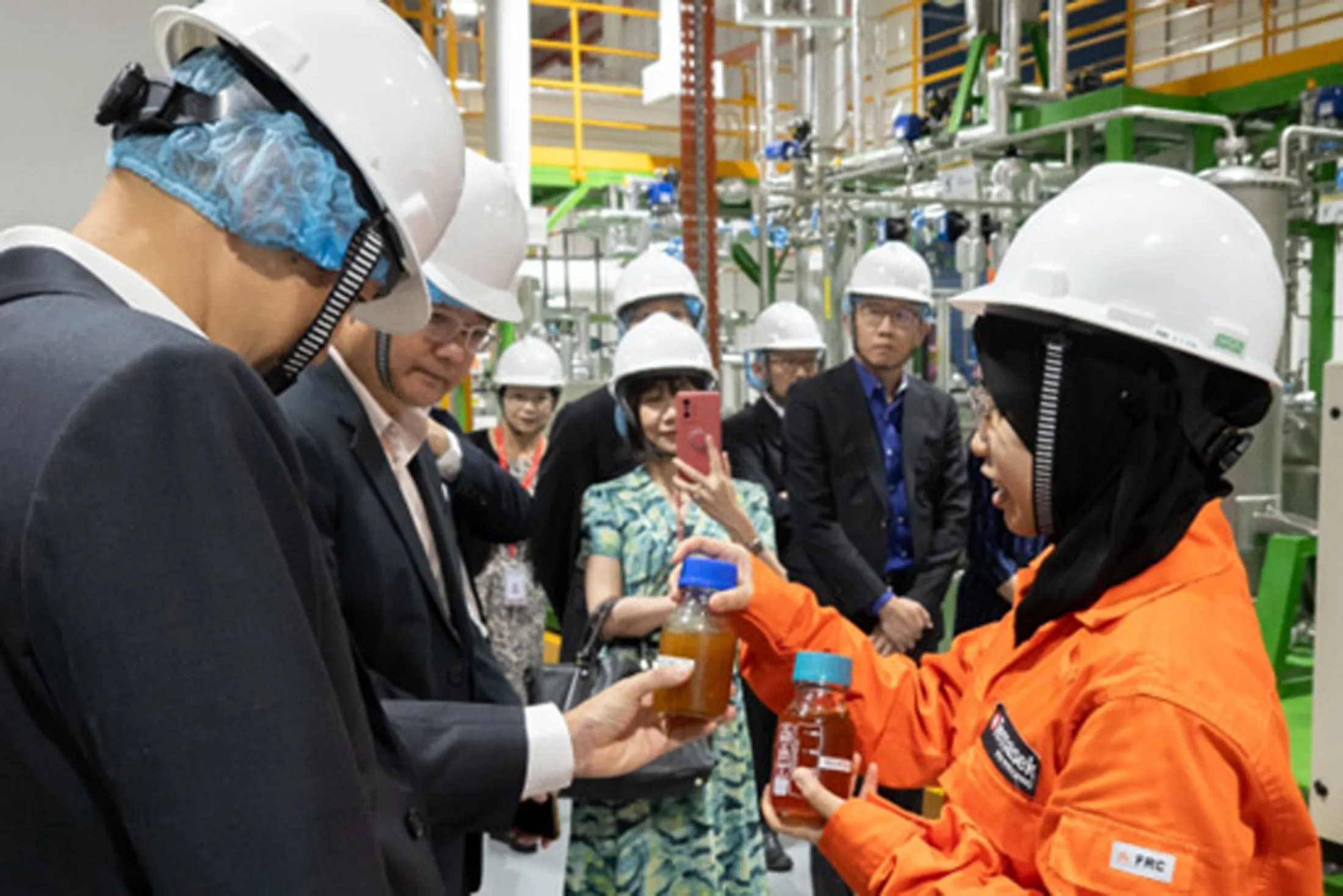
Annex
About Temasek Polytechnic’s Chemical Pilot Plant (CPP)
Temasek Polytechnic’s (TP) new integrated Chemical Pilot Plant (CPP), housed within TP’s School of Applied Science places an emphasis on applied learning and aims to equip our learners with skills for the future economy. The new CPP was constructed to meet industry standards and provide relevant training for the Diploma in Chemical Engineering students.
The CPP offers a comprehensive view of the processes within a chemical plant. It is organised into four sectors: Biodiesel Production, Wastewater Treatment, Safety Corner, and Distributed Control Room. Each unit operation can be isolated for standalone learning and allows for concurrent batch operations of multiple units, as well as continuous flow processes. The plant features Augmented Reality for enhanced visualisation, immersive training, and interactive learning experiences.
These are the four sectors of the CPP and its features:
(i) Biodiesel Production
The CPP is the first industry-standard plant in an institute of higher learning in Singapore to convert waste cooking oil into biodiesel. An official service agreement had been signed between TP and Alpha Biofuels to collaborate in producing this biodiesel.
This sector includes reactors and separation units such as liquid-liquid extraction, ion-exchange columns, gas absorption, and distillation columns. Students learn about esterification and transesterification reactions to convert waste cooking oil into biodiesel. The separation units mimic industry practices for impurity removal to produce biodiesel.
(ii) Wastewater Treatment
This sector allows students to explore essential processes for environmental sustainability. The treatment process includes:
- Pre-treatment: Conditioning, neutralisation, coagulation, flocculation, and dissolved air flotation.
- Secondary treatment: Trickling filter, advanced oxidation, and sedimentation.
- Final stages: Granular filtration, carbon absorption, ion exchange, ozone generation, and UV disinfection.
(iii) Safety Corner
Addressing workplace safety concerns, this sector includes platforms for teaching work-at-height and confined space safety. It emphasises good workplace safety practices that are crucial for the chemical industry.
(iv) Distributed Control Room (DCS)
The DCS features a network of computer-based workstations for monitoring and remotely controlling all processes. The Human-Machine Interface and control algorithms are essential for automatically controlling key operating parameters and enabling interactive operations within the plant.